PULSEROLLER's Motorized Drive Roller Conveyor Systems
The Future of Smart Conveyor Design
Motorized drive roller (MDR) conveyor sections are sections that utilize a single motorized conveyor roller that is only mechanically linked with enough free-turning (gravity type) rollers to constitute a controllable zone. This zone is usually not much longer than the item to be conveyed. With the proper control system strategy, you can easily assemble individual MDR zones like building blocks to make zero pressure accumulation conveyor sub systems, particularly for traditional carton type handling applications.
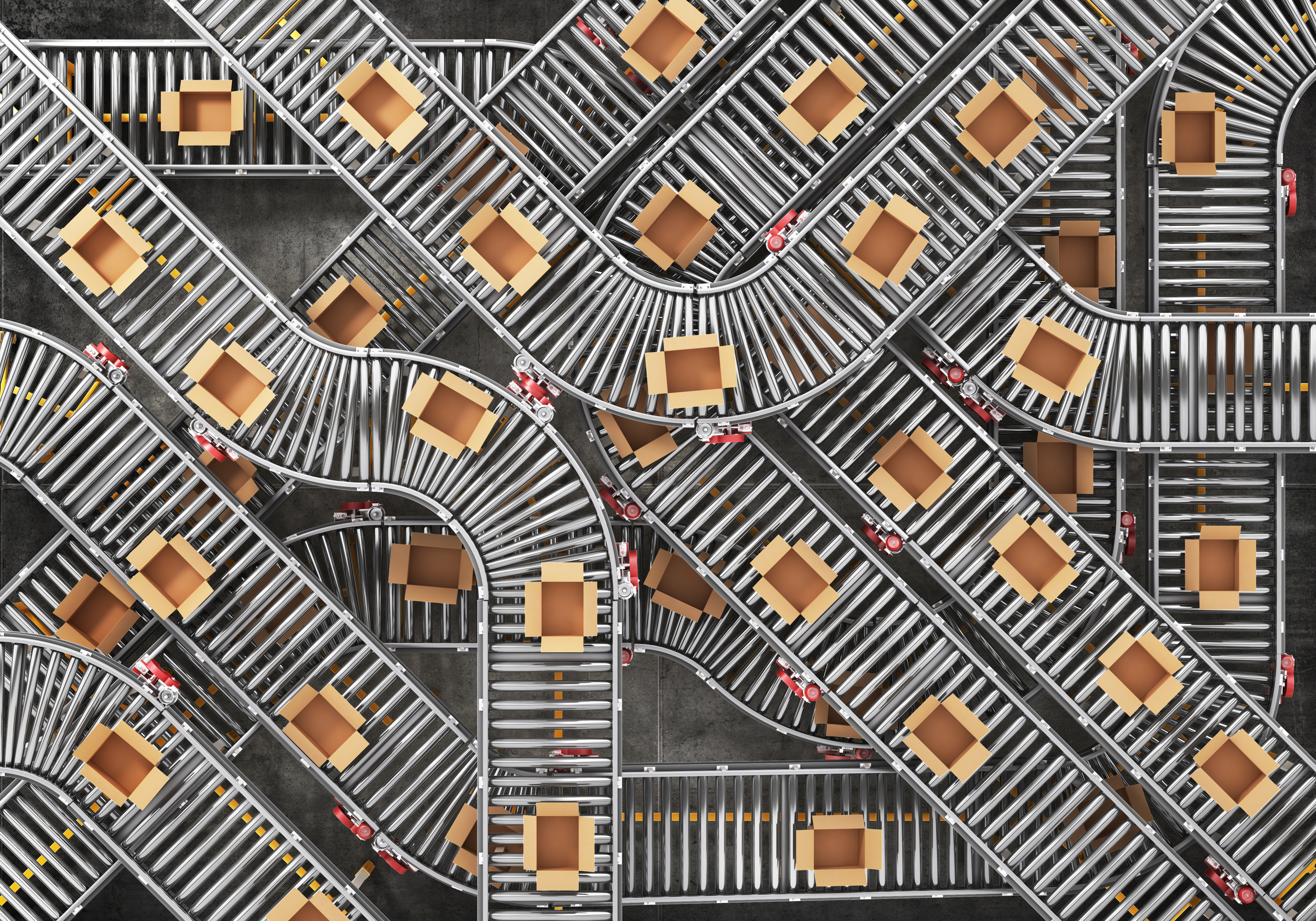
MDR conveyor sections with the proper control system strategy are inherently modular, both mechanically and electrically. Instead of having a single 100-ft. accumulation conveyor with its big 5HP, 480-volt gear motor, and its own air feed drop; you now have 10 manageable 10-ft. modular accumulation sections that connect together. You don't have to supply air piping, and your power sourcing can be as simple as plugging into a standard 120-volt household wall receptacle.
MDR Means Energy Savings
Typically, conventional conveyors run all the time whether they are accumulating product or not. One of the greatest aspects of motorized drive roller conveyors is the fact that, with the proper control system strategy, MDR zones only run when they need to. In a typical MDR system, the rollers in any given zone only run 10% to 50% of operational time. You could realize a savings of 30% to 70% in energy savings alone, which means a faster return on investment for your business.
MDR Means Safety
Large, conventional motors can be extremely dangerous for your warehouse personnel. A stray hand, limb, or piece of clothing can lead to tragic injury if caught up in a bad place or pinch point while the conveyor is running. In addition, such motors use tremendous amounts of power, which can also present warehouse dangers. The motorized drive roller in a typical MDR zone is powered by 24 volts DC, and has no major pinch points. Moreover, MDR only has to provide motive power and torque to a short zone, so there is never enough drive power to be dangerous. In most cases, you can literally grab a running motorized roller with your bare hand and make it stop with only a handshake grip.
Motorized drive rollers can help protect your ears, as well. MDR conveyor systems are much quieter than conventional conveyors. Conventional conveyor usually uses chains and sprockets somewhere in its drive train. Vibration is then transferred to conveyor frames, supports, and rollers, and the resulting noise can be a significant hazard. To make matters worse, in most conventional systems, the motor and drive train runs all the time, so you have chain noise and vibration whether or not you are conveying or accumulating product. Motorized drive roller conveyors operate relatively quietly, and only run when necessary. MDR systems typically achieve noise levels of 70dB or less.
MDR Means Plug and Play
The phrase "plug and play" has become ubiquitous in product marketing. Many companies and products promise you "plug and play" because it sounds nice, but fail to deliver the "plug" or the "play." Motorized drive roller conveyor systems make "plug and play" a reality.
With the proper control system strategy applied up front, a typical motorized drive roller section is electrically pre-wired at the manufacturer prior to shipment. A typical section will utilize plug connectors at each end to allow the unit to be set in place and simply plugged into the unit in front of it and the unit behind it to make it operational.
As a result, you can easily add or remove sections of conveyor as needed to alter or re-route your conveyor path (even temporarily) to accommodate the changing needs of your business. Also, with the proper control system strategy applied, this endeavor need not require a gaggle of engineers, programmers, or technicians to accomplish. In some cases, your own people can make changes and modifications with minimal assistance from the original conveyor equipment or control system provider.
MDR Means Lower Maintenance Cost
The inherent advantages of motorized drive roller conveyor design mean your maintenance and spare parts costs are dramatically lowered.
Because MDR conveyors only run as needed, there's less wear and tear to the component parts. Most of the maintenance and wear associated with conventional conveyors comes from the drive train (sprockets, chains, belt lacing, etc.). Even the most modern and efficient gear motors require regular maintenance and lubrication.
The typical motorized drive roller, however, utilizes sealed for life bearings, which means much longer base equipment life. Moreover, for any given system, most of the motors will be interchangeable, which means you only have to stock one spare part. Contrast this with the typical conventional system where gear motors can differ greatly in size within a single conveyor system, each one needing its own stock of spares, and the advantage of going with MDR is clear.
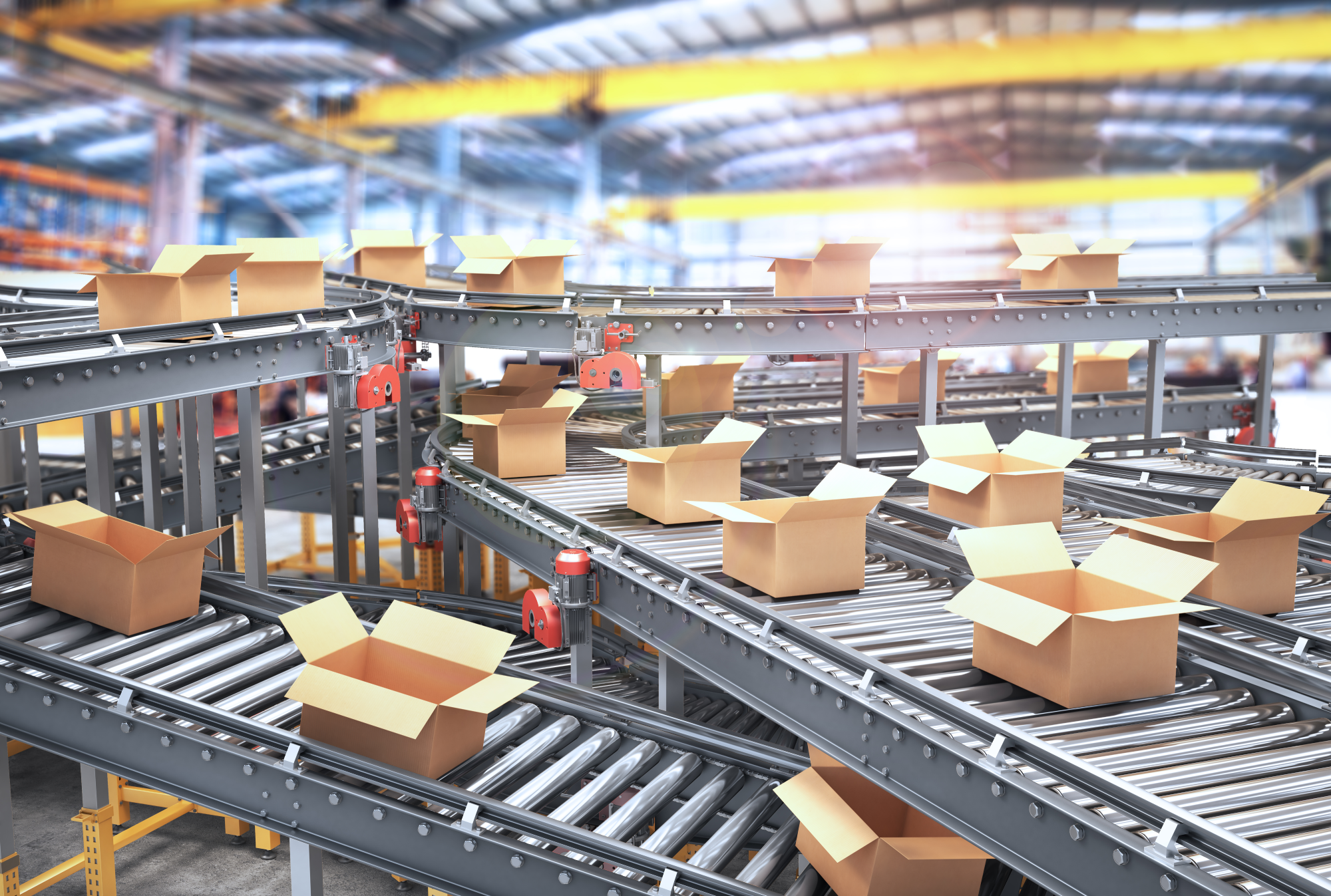
MDR Is the Coming Standard
Most conveyor manufacturers have embraced the motorized drive roller conveyor concept in one form or another. As time goes on, motorized drive roller products are being placed on the market to solve traditional material handling functions other than just zero pressure accumulation. There are currently several versions of merges and transfers on the market, and there's more to come.
Proper Control System Strategy
The right design concept is the key to getting the most out of your MDR conveyor system. The conveyor equipment industry provides the mechanical building blocks and tools to move materials, but the control system is what makes it go, slow down, speed up, and stop when you need it to. The ideal control system for motorized drive roller conveyor is distributed within each conveyor section, because each section only needs to know what is going on in front of it, and only needs to tell the section behind it what it's doing.
Control strategies that allow for data and information handling within an MDR control system further open the door to utilizing MDR solutions by enabling more intelligent functionality, such as product tracking and sorting. Until now, these things have been the sole province of conventional conveyor systems with custom control systems.